Decarbonization initiatives are gaining momentum in the construction industry as this sector seeks to reduce its massive carbon footprint. According to World Green Building Council estimates, the construction industry is responsible for generating an estimated 39% of the world’s carbon emissions with 11% of that coming from embodied carbon emissions, or ‘upfront’ carbon that is associated with materials and construction processes throughout the whole building lifecycle.
While it is clear that the energy-intensive construction industry has a lot of ground to cover when it comes to sustainability, common misconceptions about the high cost of materials for reducing embodied carbon are slowing progress. These misconceptions are refuted in new research which shows that reducing embodied carbon in construction does not have to cost more.
The study, conducted by global construction and asset management consultancy Currie & Brown, systematically compared the installed costs of exterior wall assemblies commonly used in industrial buildings to determine whether low-carbon material choices cost more.
Researchers examined the installed costs of a specific insulated metal panel (IMP) wall system, insulated precast concrete and tilt-up concrete wall systems, in typical warehouse or light manufacturing buildings of around 150,000 sf gross floor area in a total of 18 cities across the United States and Canada.
Results from the research clearly show that the specific IMP wall system costs less to install in industrial buildings than both insulated precast concrete and tilt-up concrete wall systems. Cost savings were demonstrated across all 18 cities evaluated in the US and Canada, with average potential savings between 18% to 32%, depending on location.
According to this analysis, cost savings of sustainable material selection can really add up. The applied total cost savings of using the IMP system in the example 150,000 square foot industrial building, instead of concrete wall systems, range from $279,941 in St. Louis compared to tilt-up concrete walls, up to $540,324 in Seattle, compared to insulated precast concrete.
Earlier research by architectural research and planning firm KieranTimberlake also refutes the perception that low-carbon material choices cost more. This study examined IMPs with a specific type of insulation core, insulated concrete, tilt-up concrete and mineral fiber IMPs in the design of a virtual industrial building in Philadelphia to compare their impact on embodied carbon. The analysis found that specific type of IMPs were clearly a lower carbon choice, containing 28% less embodied carbon when compared with traditional concrete wall assemblies.
To make significant progress in the drive toward sustainability, the construction industry will need to more widely embrace green building materials and practices. Moving away from the selection of building materials like concrete that produce high levels of carbon emissions will play a major role in reducing the construction industry’s carbon footprint. That’s because concrete production is one of the world’s largest sources of carbon emissions – the production of cement, a key ingredient in concrete, accounts for about 8% of the world’s carbon dioxide emissions.
Insulated metal panels (IMPs) are a good alternative. They aid net zero energy and carbon-neutral efforts by producing an airtight, moisture-resistant, rigid, continuous-insulation envelope. IMPs offer high R-values and provide superior thermal performance and reduced operational energy costs. Ultimately, this results in fewer greenhouse gas emissions and reduced energy costs.
Research confirms that making greener building envelope material choices doesn’t have to cost more. IMPs should be the cladding material of choice for saving costs, reducing embodied carbon and improving building performance.
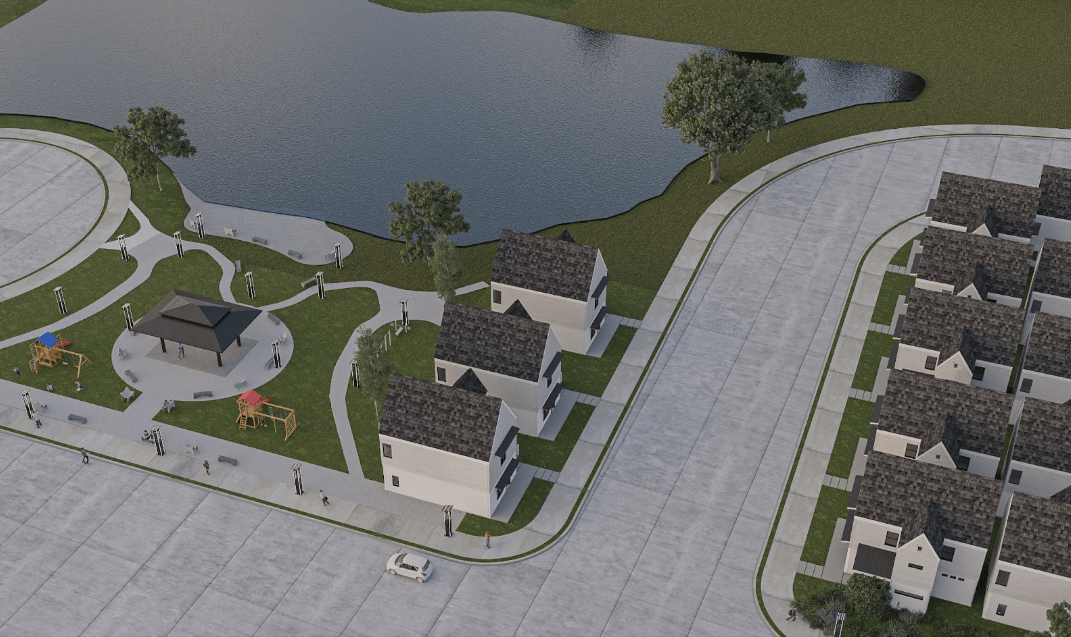